TK Elevator’s cloud-based smart maintenance – for which EOX comes “plug and play”-ready – provides intelligent data analytics packaged to fit your service needs. It results in enhanced service quality, less paperwork, real-time equipment transparency and increased peace of mind.
Smart and easy maintenance
Through its smart sensors and connected components EOX can collect real-time data to calculate the remaining lifetime of each of the elevator’s key components, determining which parts will require maintenance, a readjustment, a repair or a replacement – and when. Door movements, speed, number of trips and power-ups, car calls – all this and more is aggregated and sent to the cloud where algorithms analyse it for patterns and determine the “health” of your elevator. This data-driven approach has the power to cut elevator downtime by up to 50%.
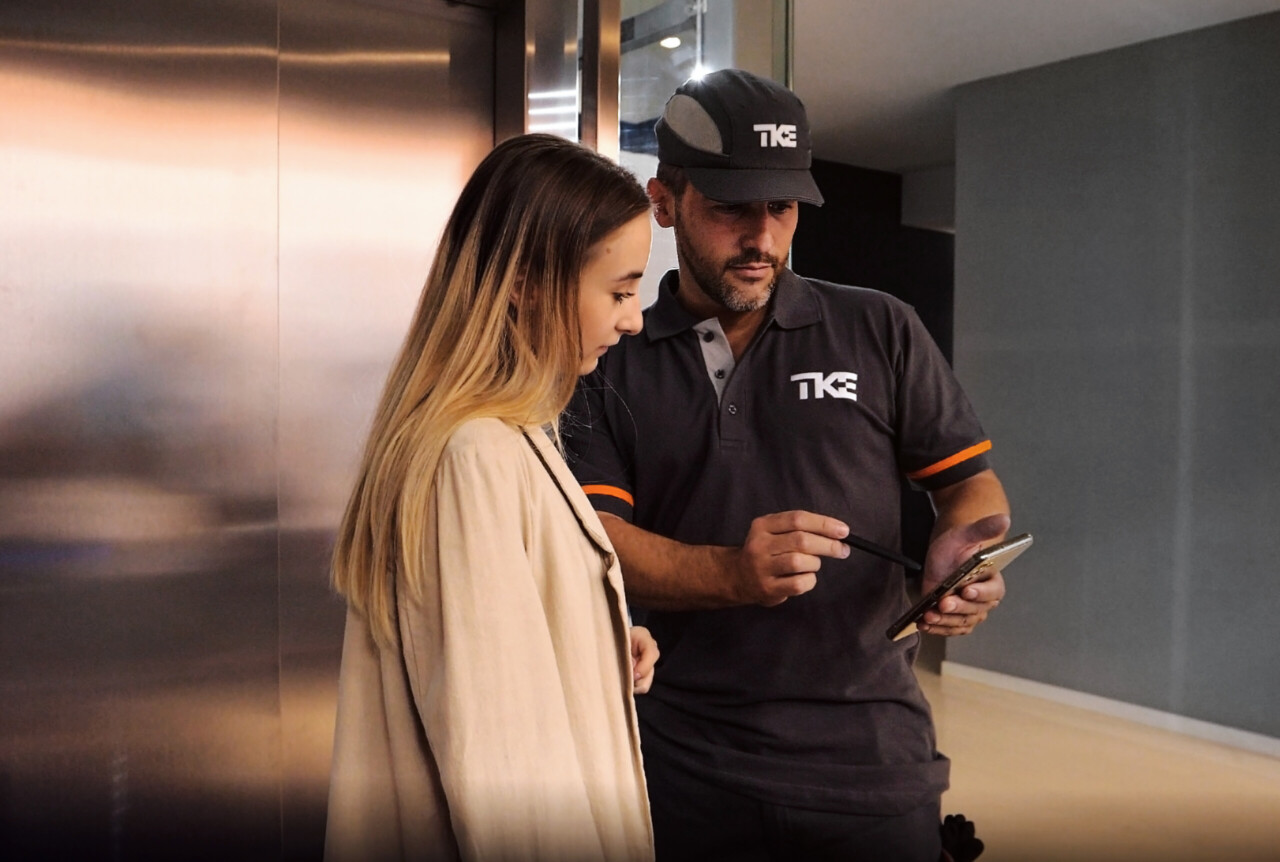
And the best thing about it: It’s at the fingertips of all parties involved – for the owner or a building manager through the included TK Elevator Customer Portal, as well as the service technician in charge of the elevator. Independent of the type of maintenance contract with TK Elevator, every EOX owner benefits from advanced troubleshooting as well as notifications and critical alerts. Performance data and diagnostics delivered to our technicians in real time indicate where intervention is required. The pre-defined notification contacts are also informed about any incidents. What does that mean for you? Maximum transparency, fewer unscheduled visits, quicker clearing of breakdowns or malfunctions and increased uptime for passengers and tenants.
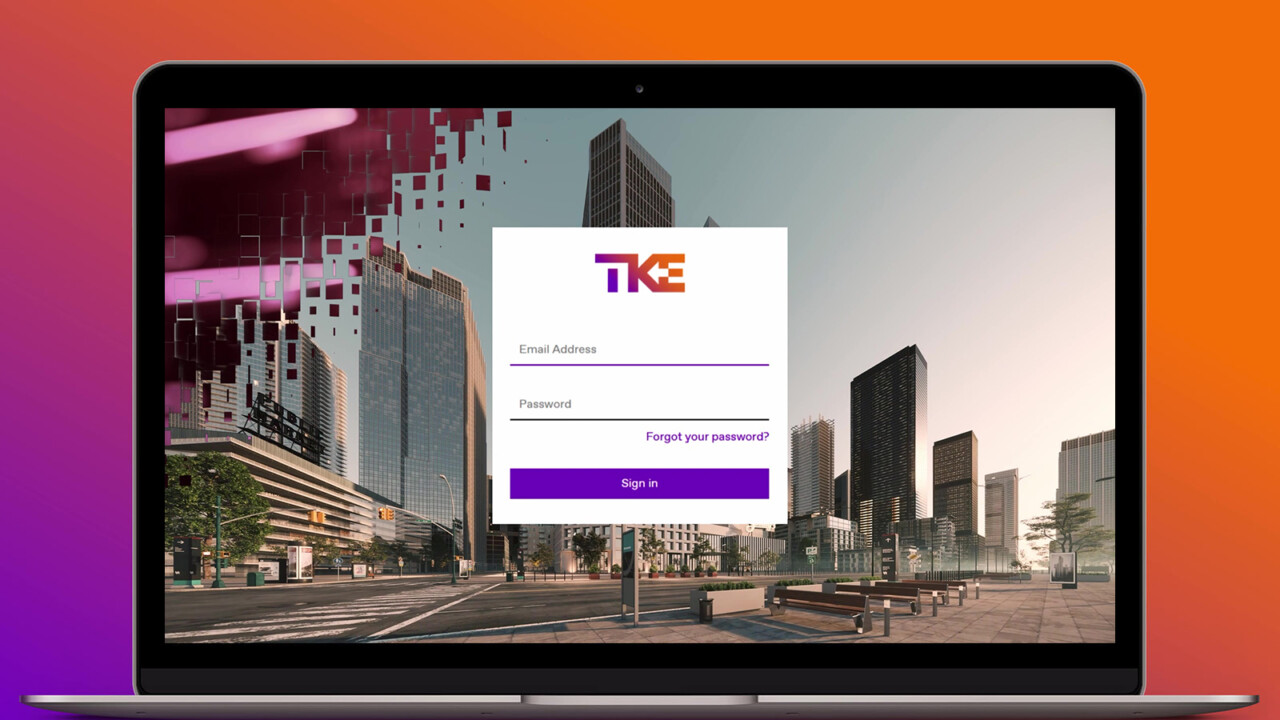
TK Elevator was the first to introduce the elevator industry to a fundamental shift from reactive to proactive maintenance. With EOX, this is now a standard for even the most basic everyday elevators. Our first-mover advantage combined with cutting-edge cloud technology, IoT connectivity and Big Data analysis gets you more transparency, prolonged lifetime for your units, and enhanced safety and reliability for your passengers.
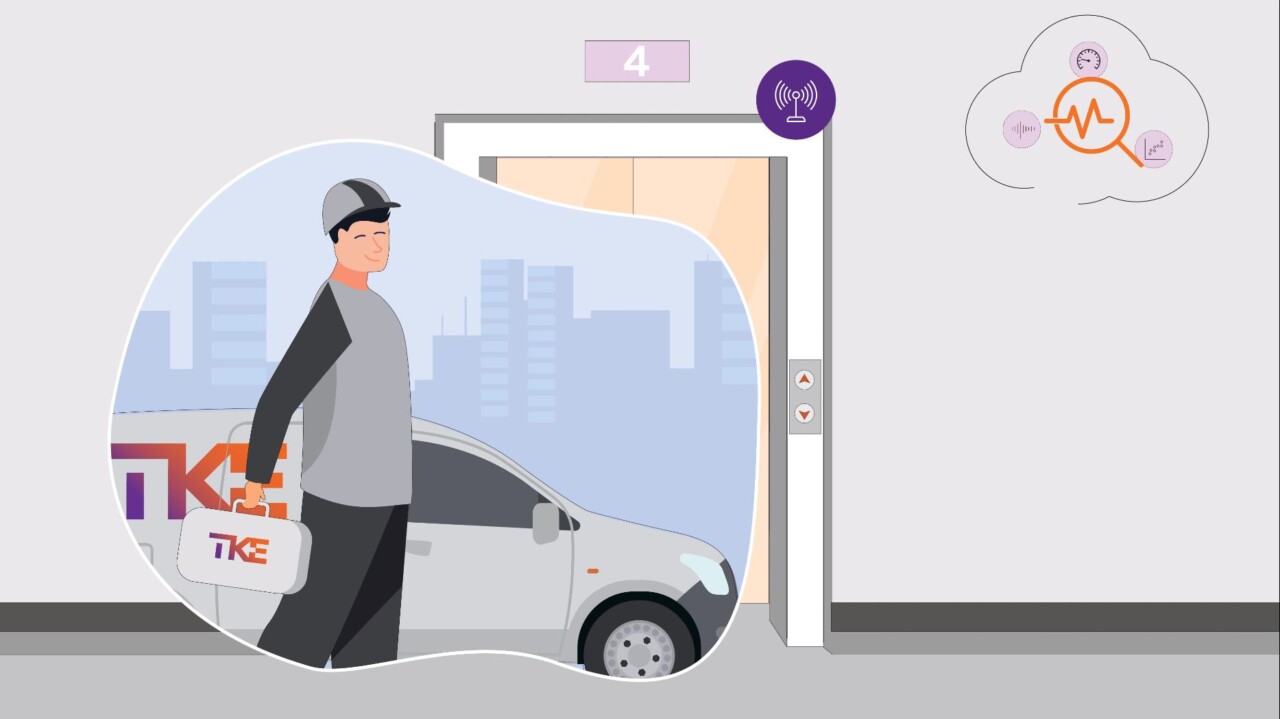